Battery packs generally refer to packaging and assembly of batteries. For example, we connect two lithium batteries in series and form a specific shape according to customer requirements. We call it PACK.
The PACK grouping process is a key step in the manufacturing of power battery packs, and its importance is becoming more and more obvious as the electric vehicle market continues to expand. At present, the battery PACK industry is still an emerging industry in China. The technology and equipment are still developing, the overall quality of technicians is not high enough. Its high technical threshold also makes it difficult for companies to enter the industry. The “Power Lithium Ion Battery Pack Production Process Training” to be held in Tianjin will help solving these problems. It is understood that this is a training course for technicians in the front line of the power battery PACK industry. It will provide detailed training on the connection process, packaging process, welding process and injection molding process in the battery PACK process, and will also explain the power battery system. Design, power battery pack off-line detection, various problems and solutions in the actual production process.
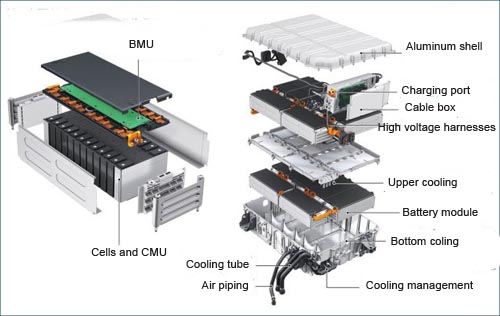
power battery pack structure
Automotive power battery structure
1) Power battery module
Needless to say, if the battery PACK was a human body, then the module shall be the “heart”, responsible for storing and releasing energy to power the car.
2) Structural system
The structural system is mainly composed of battery PACK cover, tray, various metal brackets, end plates and bolts. It can be regarded as the “bone” of a battery PACK, which plays the role of resisting mechanical shock, mechanical vibration and offering environmental protection (waterproof and dustproof).
3) Electrical system
The electrical system consists mainly of high voltage jumpers or high voltage harnesses, low voltage harnesses and relays. The high-voltage harness can be regarded as the “aortic blood vessel” of the battery PACK, which continuously transmits the power of the heart of the power battery system to each required component. The low-voltage harness can be regarded as the “neural network” of the battery PACK. Besides, the detection and control of signals are transmitted in real time.
4) Thermal management system
There are four main types of thermal management systems: air-cooled, water-cooled, liquid-cooled, and phase change materials. Let’s take the water cooling system as an example. The thermal management system is mainly composed of a cooling plate, a cooling water pipe, a heat insulating mat and a thermal pad. It is equivalent to installing an air conditioner for the battery PACK.
Some people will ask, why does the battery need a thermal management system? In fact, the answer is very simple, because the process of charging and discharging of the battery is actually the process of chemical reaction. The chemical reaction will release a lot of heat, and the heat needs to be taken away, so the battery is working in a reasonable temperature range, which improves the life cycles and reliability of the battery.
5) BMS
BMS: Battery management system. It can be seen as the “brain” of the battery, mainly be composed of CMU and BMU.
CMU: Cell monitoring unit,
It is responsible for measuring the voltage, current and temperature parameters of the lithium polymer battery, as well as balancing and other functions. When the CMU measures the data, it transmits the data to the BMU through the battery “neural network” mentioned earlier.
BMU: Battery management Unit.
It is responsible for evaluating the data transmitted by the CMU. If the data is abnormal, the battery is protected, and the current will be reduced, or the charge and discharge path will be cut off to prevent the battery from exceeding the permissible use conditions. Meanwhile, the battery power and temperature are also managed. According to the control strategy previously designed, the parameters and status that need to be alerted are determined, so the warning is sent to the vehicle controller and finally to the driver.
In the battery pack, the BMS (Battery Management System) is the core, which determines whether these components and functions of the battery pack can be coordinated, and directly relates to whether the battery pack can provide power output for the electric vehicle safely and reliably. Of course, the connection process, space design, structural strength, and system interface of the structural members also have an important impact on the performance of the battery pack.
In short, the PACK group process level of the battery pack is directly related to the power performance and safety performance of the electric vehicle. We can say, whether the power battery pack can perform well is a matter of life and death